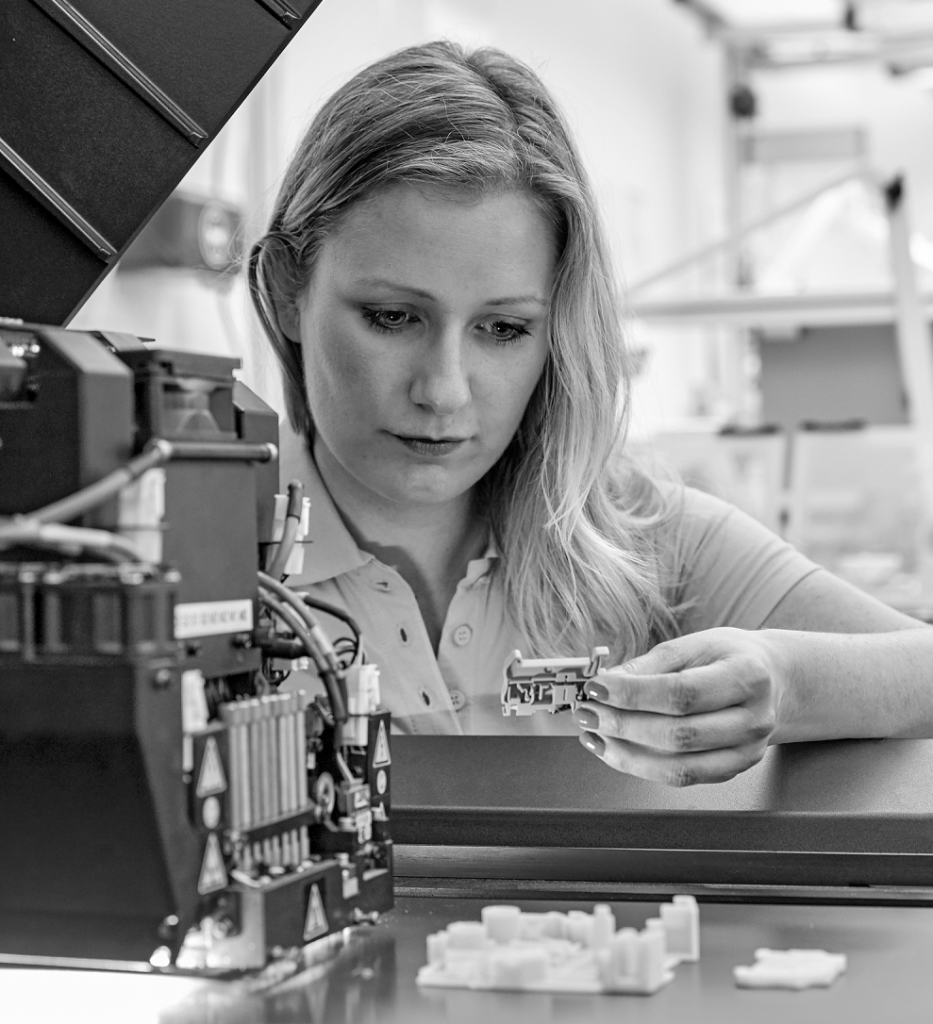
Step by Step to A 3D Object Made of Ceramic
Lithography-based Ceramic Manufacturing (LCM) is an additive manufacturing process that, as the name suggests, is based on the 3D printing process of stereolithography.
The still young technology enables the production of high-resolution and detailed 3D objects with the desirable properties of technical ceramics.
In contrast to 3D printing in plastics, ceramic components are produced in several stages. In order to be able to print objects in ceramics, a so-called green body is first produced using the stereolithography process. This consists of a mixture of ceramic powder and a light-sensitive monomer, which is worked into liquid slurry.
The print head of the 3D printer is lowered and immersed in the suspension. UV light activates polymerization so that the material hardens at the coordinates specified by a CAD file. This creates the desired shape layer by layer.
The object receives its final properties in a subsequent multi-level treatment: In the thermal debonding process, the plastic components, which are only required as aids for the construction of the green body, are removed from the green body at temperatures of up to 1,600°C. The workpiece receives the hardness and smooth surface typical of ceramics in a final sintering process.
Heat-Resistant Metal Replacement
Materials used in the LCM process are characterized by their exceptional temperature-resistance. The most widely-used substance, aluminum oxide, withstands heat up to 1,600°C. Bioresorbable substances such as tricalcium phosphate are particularly attractive for the medical sector.
Material for Extraordinary Requirements
Properties such as special temperature-resistance and a pronounced electrical insulation capacity make 3D printing in ceramics attractive for application in high-temperature technology. Low weight and high wear-resistance make it ideal for application in mechanical engineering, aerospace and medical technology.