Wear-resistant and temperature-resistant:
These materials are used in lithography-based ceramic manufacturing.
Aluminum Oxide (Al2O3)
Aluminum oxide (Al2O3) is the most widely used material in ceramic 3D printing. The oxide ceramic material is processed in various purity grades, but the rule is: the purer the material, the more resilient the components. With a purity grade of 99.8%, aluminum oxide achieves a compression strength of 4,000 MPa and copes reliably with applications involving temperatures up to 1,500°C. This versatile material is frequently used for cooling elements, isolators and tools in forming technology.
Zirconium Oxide (ZrO2)
Zirconium oxide ceramics are known for their extremely high thermal expansion and resistance to cracking. These characteristics have earned the material the nickname of “ceramic steel”. Because of its high resistance to wear and high temperatures, this technical material is particularly suitable for the production of vehicle components: exhaust flaps or slide rings made of zirconium oxide easily withstand high temperatures and extend the service life of components that are under continuously heavy strain. As its surface properties are very similar to those of natural tooth enamel, zirconium oxide is also used in dental technology to make tooth implants, bridges and crowns.
Tricalcium Phosphate (TCP)
The osteoconductive and bioresorbable properties of tricalcium phosphate (TCP) make it a functional material for bone replacement. So-called scaffolds can be made from it, for example, given an individual shape and complex pore structure by 3D printing. These are used as implants for larger bone defects. In the course of the healing process, the material breaks down in the body and simultaneously encourages the formation of natural bone.
Advantages
- extremely corrosion and wear-resistant
- smooth surface
- suitable for use in the food industry
- easy to process
- worldwide availability and low price
Advantages
- extremely high resistance to cracking
- low thermal conductivity
- high thermal expansion
- well-suited to ceramic-steel combinations
Advantages
- implants made for individual patients
- high compression strength with low weight
- supports the healing process
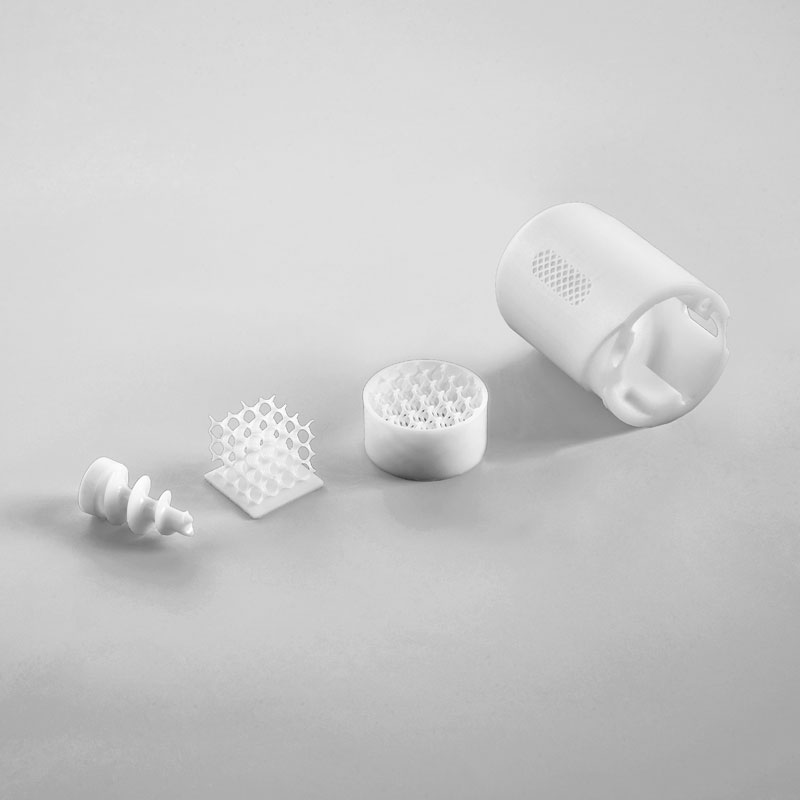
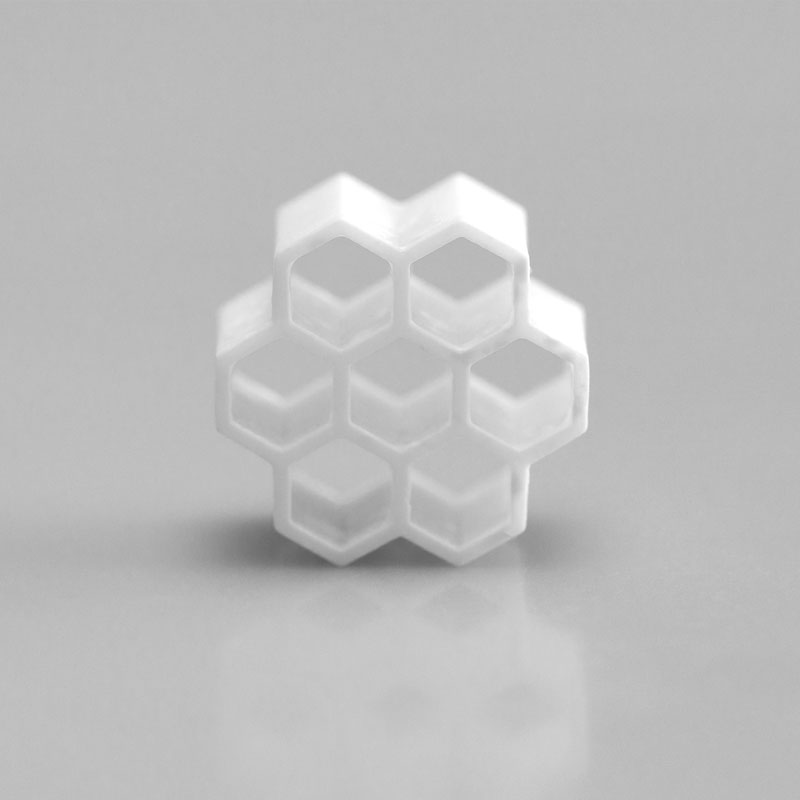
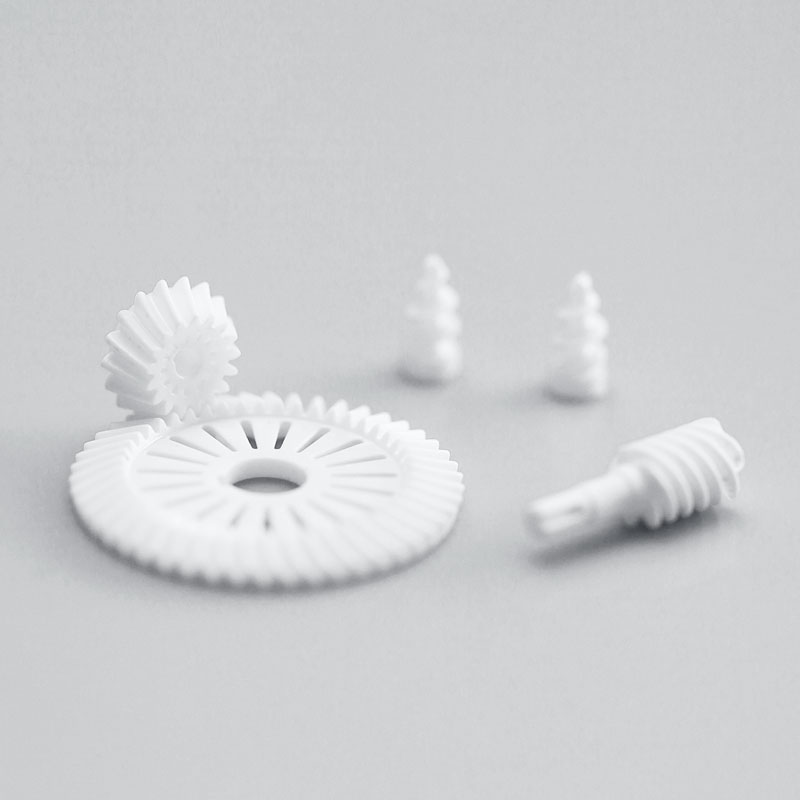