Ceramics – a challenge for 3D Printing
In additive manufacturing, ceramic materials are more difficult to process than the established plastic and metal-based materials. Ceramic particles can be melted and processed into solid bodies only at extremely high temperatures (> 1,600°C). As a result, pure ceramic components cannot be produced with the necessary density and hardness with standard additive processes such as selective laser sintering (SLS) and laser melting (SLM). In order to combine the advantages of 3D printing with the many positive material characteristics of ceramics, 3D objects are produced in a multi-stage process. Lithography-based ceramic manufacturing (LCM) is used to make precise, high-quality components from ceramic materials, which are used, for example, in micro-electronics, plasma technology and high-temperature applications.
From green body to precision work of art
In the first production stage a green body is constructed from a ceramic monomer solution. For this the liquid used in the stereolithography process is hardened with UV radiation layer by layer until the planned shape is complete. The UV radiation triggers a polymerization process by means of which the plastic components in the suspension combine and solidify, allowing them to be built up to make a 3D object. The finished green body is made partly of ceramic, partly of plastic. To obtain a pure ceramic object, the plastic components are then removed from the product by thermal debinding: the plastic is broken down at temperatures of up to 1,600°C, leaving behind a porous ceramic body. In a final sintering process the component is compressed, creating a 3D object with over 99% of the theoretical density. During the sintering process the ceramic body shrinks. This fact must be taken into consideration when planning the object to allow the end product to remain within the specified tolerances. Usually the change in size caused by the post-treatment is calculated automatically by the CAD software.
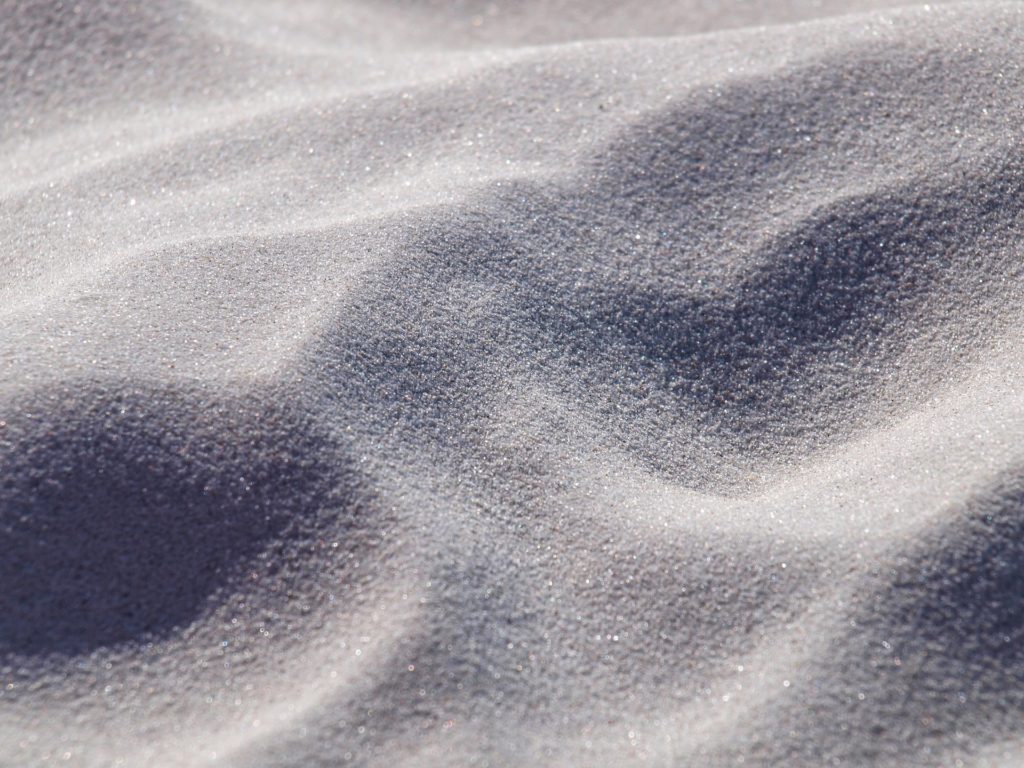